FLSmidth was chosen as the preferred provider for four large bolted thickeners for a large customer in Mozambique. Two of the thickeners are designed to reduce water load on the filters allowing for a drier filter product, while the other two thickeners recover water from the plant tailings.
Large FLSmidth bolted thickeners for Mozambique plant
The installation, which includes E-Volute™ feedwell technology for superior flow distribution, will contribute to achieving optimal water balance in the customer’s coal plant in Mozambique.
Measuring 45 metres in diameter, the thickeners will assist in achieving a drier product from the filter plant and control the density of material to the belt filters. According to Howard Areington, FLSmidth’s General Manager for Capital Sales in Sub-Saharan Africa, this will improve the plant’s output.
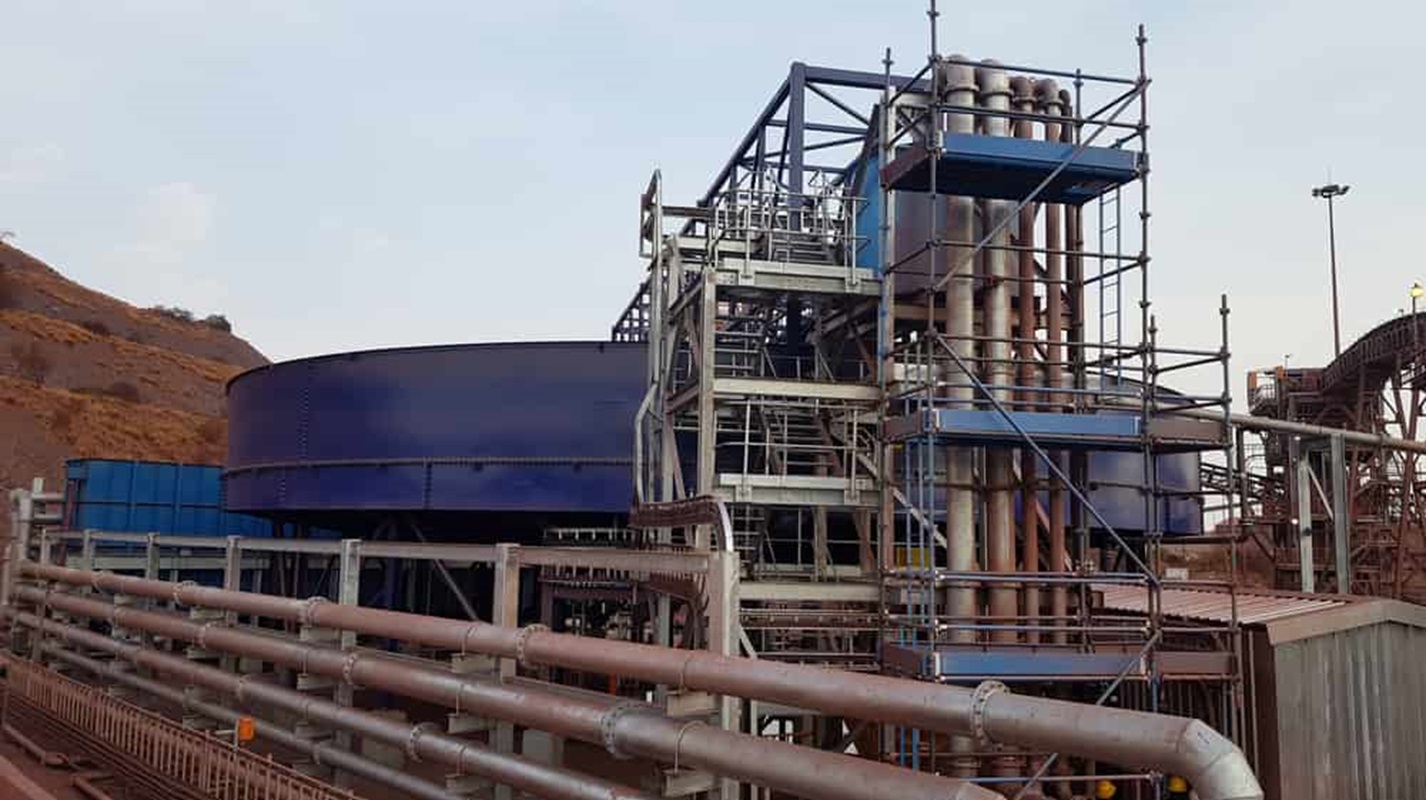
“Our test work on the material to be treated gave us the scientific basis for determining the best thickener solution, including the size of the tanks. This data was then incorporated in the structural and mechanical elements of the design.”
HOWARD AREINGTON
General Manager for Capital Sales in Sub-Saharan Africa
An important aspect of a bolted thickener is that its construction is quicker and safer, he says, requiring only a fraction of the welding to be conducted on-site. This suits the conditions for the project, which is remotely located.
The extent of welding in the construction of normal steel thickeners typically runs into kilometres. It is far more cost effective to do this in controlled workshop conditions, where quality can also be better managed. By contrast, the amount of on-site welding required by a bolted thickener can be measured in metres.
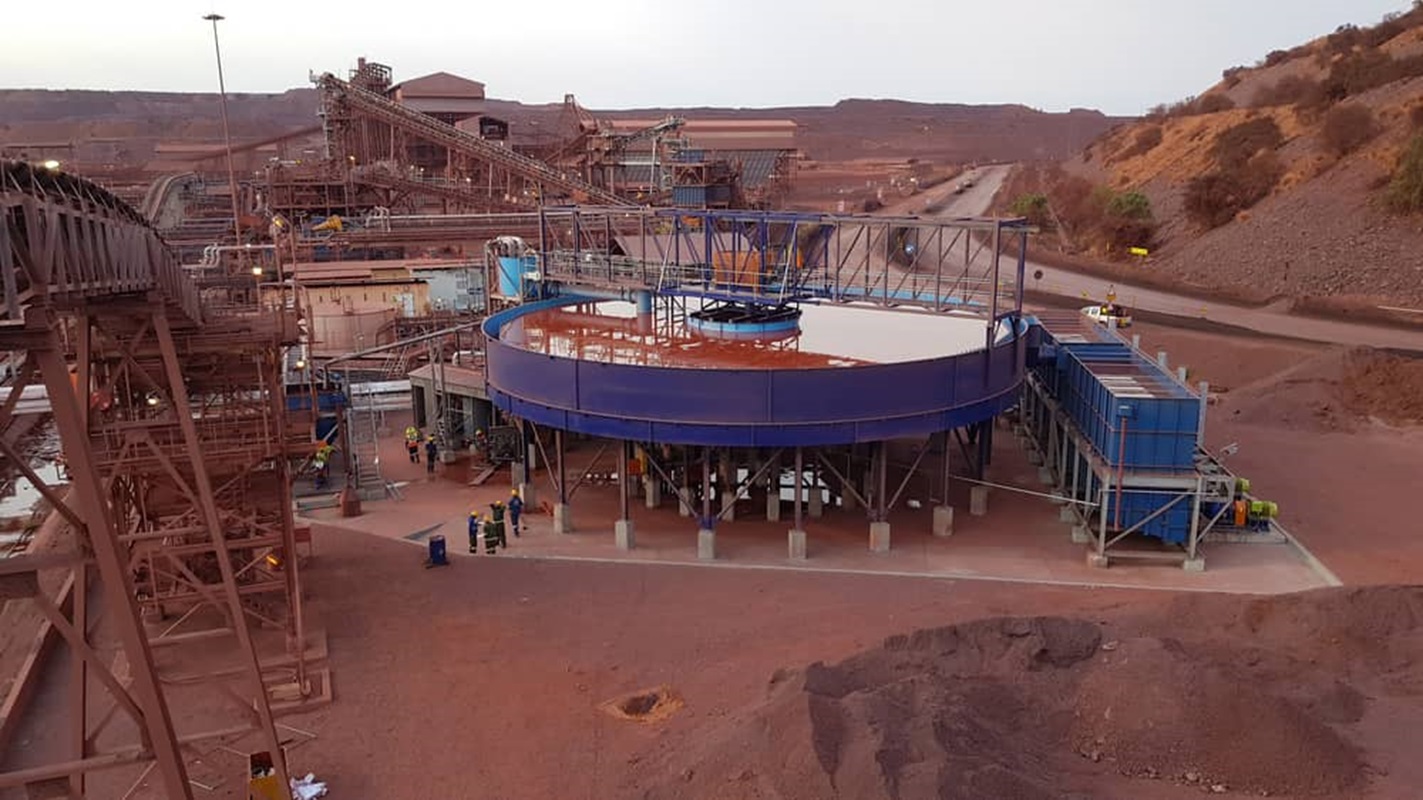
"FLSmidth’s bolted thickener technology has been embraced globally, especially in areas where installation costs are high. Australia still has the highest number of FLSmidth bolted thickeners, but the technology has steadily been adopted around the world with multiple installations in southern Africa, Europe and South America.”
HOWARD AREINGTON
General Manager for Capital Sales in Sub-Saharan Africa
As mentioned, the thickeners include E-Volute™ feedwell technology for superior flow distribution. This leads to lower flocculant consumption, better settling rates and improved overflow clarity for the optimal performance of the thickener.
“Controlling the cost of flocculant – the single most important reagent in this process – is key to our thickener design,” he says.
Despite the COVID-19 lockdown, good progress was made on the fabrication of the thickeners in South Africa, according to FLSmidth Project Manager Kevin Kockott. This has been managed by leveraging FLSmidth’s global resources and the design teams’ ability to work remotely.
“Our local South African office collaborated closely with our engineering hub in Salt Lake City in the United States, ensuring that our engineering work on the project was able to continue without interruption. Working with a highly respected fabricator also allowed us to limit the impact of the lockdown. Good planning – including the procurement of certain materials before the hard lockdown – gave us added ability to expedite our preparations for fabrication.”
KEVIN KOCKOTT
Project Manager
The design of the thickeners features FLSmidth’s well proven bridge-mounted rake drive, known for its simplicity and ease of operation. The rake mechanism includes a proprietary low-profile style with tubular rake arms. These are able to move high-yield stress material with minimal drag and torque exerted on the drive mechanism.
Areington emphasises that all mechanical elements are designed for long life. This limits the intervention of the plant personnel to regular maintenance.
"We take particular care to ensure the drive mechanism delivers optimal uptime and delivers a lifespan of 20 to 25 years. As part of our test work, we measure the yield stress of the material as a key determinant in selecting the drive size. This is generally a function of the underflow density.”
HOWARD AREINGTON
General Manager for Capital Sales in Sub-Saharan Africa
Most of the large thickeners operating in the southern African market – up to 120 metres in diameter – have been supplied by FLSmidth. He highlights FLSmidth’s impeccable group pedigree in terms of thickeners.
“Our large installed base of units around the world is testament to our cutting-edge thickener technology,” he says. “We have also secured most of the market for paste thickeners globally.”
FLSmidth’s involvement with the Mozambique project goes back almost a decade to the first phase of the plant’s development, according to Vice President Mining in Sub-Saharan Africa, Middle East and South Asia, Alistair McKay.
“The company has provided a significant amount of processing equipment in the coal preparation plant. This partnership has been extended into the second phase, with the supply of reflux classifier technology through to pumps, screens, and feeders. We have also fulfilled the maintenance of our equipment, so we have had a team on-site for many years.”
ALISTAIR MCKAY
Vice President Mining in Sub-Saharan Africa, Middle East, and South Asia