Project: GOLD MINING
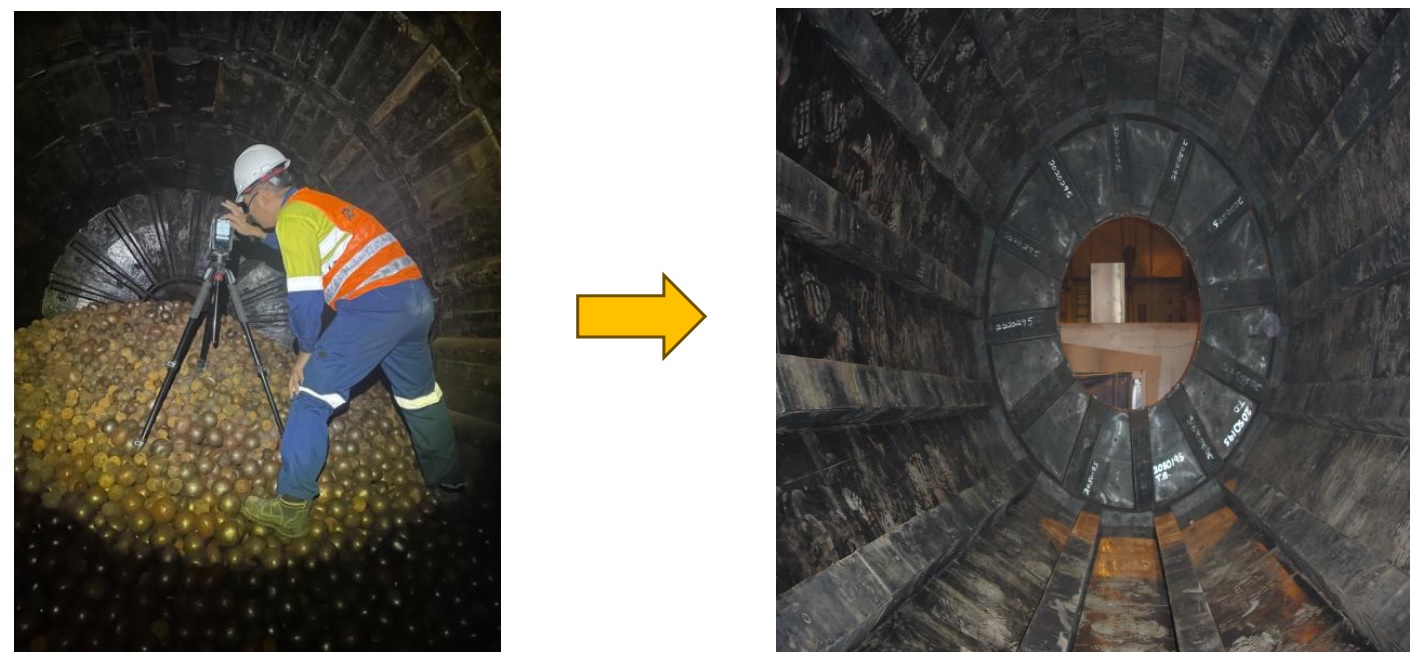
I. Advantages of using rubber/composite lining in mill.
Advantage #1. Lightweight rubber/composite liner.
It is well known that when a plant is not operating, a mine is not profitable, so it is important that operators can predict and plan for maintenance schedules. During this downtime, relining must be completed as quickly as possible and with significant human involvement, this is a high-risk operation. Composites can help overcome many of these challenges as they are up to 1/7 lighter than metal liners. This creates the opportunity to design liners that are made up of fewer, larger components, making installation faster and safer, while reducing energy consumption.
Advantage #2. Rubber/composite lining resists ball sticking, peeling, cracking and corrosion.
Factory lining suppliers have the flexibility to design liners with fewer components when they use composite materials. This has the benefit of reducing joints between liners and minimizing joint gaps that occur with steel liners due to moldability.
The downside to steel liners is that the joints are susceptible to chipping due to the impact of the grinding balls, which can make removal difficult and time consuming. In these cases, removal often involves using a hammer to dislodge the liners and may even require cutting the joints with a cutting torch. This requires more maintenance time and poses a greater safety risk to personnel, all of which can be eliminated with composites.
Rubber/composite liners have a better fit than steel liners and the rubber joints eliminate flaking, making them much easier to remove. Another advantage of a better joint with a rubber/composite liner is that it eliminates material from entering the joint and causing raceway damage and clogging of ore particles, which is common with steel liners..
n plants with screen discharge configurations, the resilience of composite screens has been demonstrated to resist obstructions caused by ore particles and crushed materials that chip away at the screen openings..
Advantage #3. Rubber/composite lining increases feed.
Many operators overlook the fact that lighter mill liners can be optimized to increase volumetric capacity, feed and cumulative grinding ore volume..
Mills with feed volume limitations may benefit from lighter rubber/composite liners allowing more ore to be fed into the crusher without exceeding the feed volume limit. Additionally, the increased wear life provided by rubber/composite liners may allow the OEM to reduce the thickness of the liner. This results in increased volumetric capacity allowing more material to be fed into the grinding mill. This in turn creates the opportunity to increase plant throughput, resulting in increased revenue for the mine.
We used a rubber/composite mill liner system to compare with a steel mill liner system under the same process conditions. The findings showed that a properly designed composite liner system can transfer the input energy (motor power) to the grinding process better than a steel system. It is reported that this site has increased gold recovery by 2%, increased mill throughput by 16-20%, improved liner life by 40%, and reduced liner system replacement time by more than 60%.
Liner design has a significant impact on both mill availability and grinding performance. By optimizing the design through new materials, significant improvements can be made to not only enhance wear resistance but also reduce liner change times, thereby positively improving availability.
Advantage #4. Rubber/composite liners have shorter delivery times.
Due to the high production losses that occur whenever a plant is shut down, it is important that plant lining deliveries are consistently on time to allow for inspection and preparation prior to plant shutdown.
Composite/rubber materials are produced faster, with consistent quality, resulting in shorter lead times. This is a major advantage for mining operations as they have more flexibility when ordering. It reduces the need for early ordering and the risks associated with storing mill liners on site longer than necessary. Transportation costs are reduced as the rubber/cpmposite lining material is lighter.
II. Plan to convert steel lining to rubber/composite lining
1 Survey to obtain data on crusher design, grinding materials, grinding balls and mill operating mode.
2 New rubber/composite liner design.
3 Fabricate rubber/composite liner samples at high wear locations for design evaluation and adjustment.
4 Evaluate sample linings and finalize designs for full lining production.
5 Install the first rubber/composite liner to operate, get improvement data for next time.
6 Complete design and manufacturing process for rubber/composite lining is optimal.
III. Reference projects.
1 Copper smelter in Lao Cai.
2 Polymetallic Factories in Thai Nguyen.
3 Gold Factories in Quang Nam.
4 Sand factories in Quang Tri.
5 Low iron sand factories in Hue.
6 Construction materials factories in Long An.