Ssangyong Cement wanted to increase alternative fuels (AF) use at its Donghae and Yeongwol cement plants. They were interested in using the HOTDISC® reactor, one of our MissionZero flagship products. But, it didn’t fit within their existing SLC calciner layouts and a conversion to an ILC calciner to increase AF firing was not economically or technically feasible. They challenged us to redesign the HOTDISC reactor to suit an SLC calciner system.
Significantly increasing the use of alternative fuels
Ssangyong Cement, like many cement producers around the world, was keen to reduce its reliance on fossil fuels and increase the rate of AF substitution. They saw the benefits of installing a HOTDISC reactor as it enables increased AF firing with very low emissions. But the HOTDISC reactor is designed for use with an ILC calciner, which Ssangyong Cement’s plants don’t have.
Both Ssangyong Cement’s Donghae and Yeongwol plants operate older style non-FLSmidth pyro systems. Each plant has several kiln lines situated very close together. These were originally built without calciners, but SLC calciners have since been added as part of a preheater tower installed in front of the kiln. In short, they have very limited space – and converting the SLC calciners to ILC calciners was impossible.
"We had seen what the HOTDISC could do, in terms of increasing alternative fuel capacity. We were willing to support FLSmidth to redesign the system to try to make it work for us. They took on the challenge – and as a result we have been able to significantly increase our alternative fuels utilisation."
SOO-HYOUNG LEE, PROCESS ENGINEER
Ssangyong Cement, PI Construction Office
Alternative fuels
The HOTDISC can handle a wide range of alternative fuels, including:
- Refuse derived fuel (produced from municipal garbage), loose or compacted
- Tyres (whole, shredded or cut into pieces)
- Paper sludge
- Lime-stabilised oil sludge (from tanker cleaning)
- Old car fragments (upholstery, dashboards, etc.)
- Dried sewage sludge
The Ssangyong Cement plants are utilising Solid Recovered Fuel (SRF), which has been pre-sorted prior to receipt at the plant, ensuring they get good quality fuels with very low moisture content.
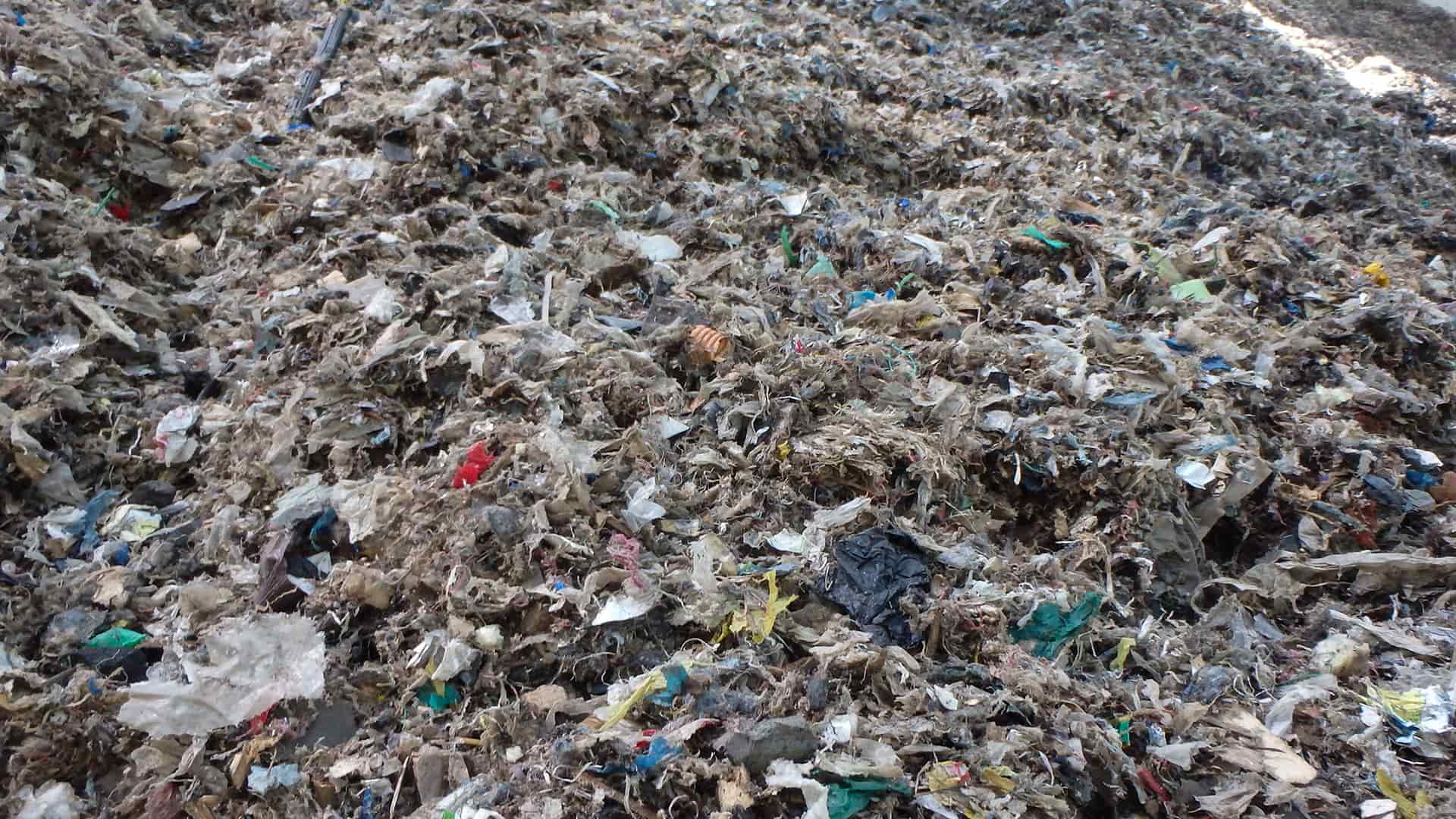
Redesigning the HOTDISC reactor
The HOTDISC reactor entered the market almost 20 years ago and has gained significant success in the last several years as cement companies worldwide look to increase AF firing as an environmental and financial benefit to their process.
The HOTDISC reactor is typically installed adjacent to the bottom of an ILC calciner and works as a slow-moving disc furnace, heated by tertiary air from the kiln. Alternative fuels – from whole truck tyres to loose RDF – are introduced onto the slowly rotating disc and begin to burn in fully-oxidising conditions when they meet the hot tertiary air. The burning fuel is transported for a turn of around 270˚, where it reaches the scraper and the remaining non-combustible ash is discharged into the riser duct. Heavy combustion residues fall directly into the kiln inlet, while lighter fragments and combustion gases move up into the calciner.
It’s a highly efficient and very low-emissions process, but one that relies heavily on the positioning of the HOTDISC reactor alongside the bottom part of the ILC calciner, above the kiln riser. The challenge for our engineers was to design a HOTDISC reactor that performs in the same way – maintaining those same efficiencies – but is positioned beneath the SLC calciner.
“It was a complex project. It’s not a totally new idea; we had thought of creating a version of the HOTDISC reactor for the SLC before – but the question was always ‘how do we get the non-combustible particles into the kiln?’,” explains Steven Miller, Global Process Line Manager, FLSmidth. “Gases can be encouraged to move in one direction or another, but heavier materials only want to fall down. And at that temperature they are difficult to transport.”
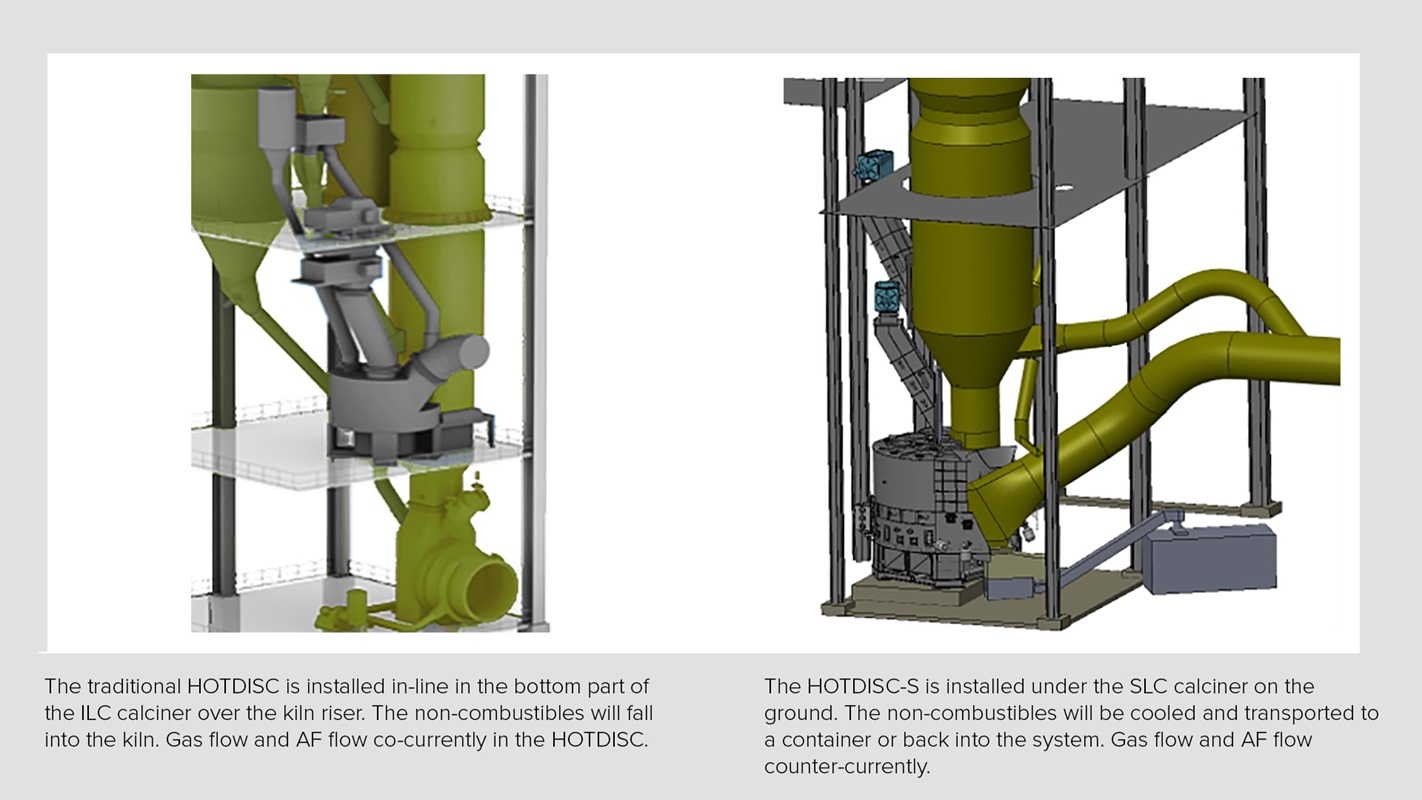
Using CFD modelling, our design team was able to work out the optimum layout to ensure the lighter particles could be lifted into the calciner and successfully burned, and to avoid the occurrence of hot spots in the chamber. The answer to handling the heavy materials came from our experiences elsewhere in the process.
“We realised that the ABC™ Inlet design that is usually used in a clinker cooler would actually be the perfect way to cool those reject particles, so that they can be transported. It takes up a relatively small area, but it works very effectively to cool material quickly,” says Steven Miller.
Success
The partnership we formed with Ssangyong Cement stipulated that if either party wasn’t happy with the results of the project, there would be no obligation to continue. But when we presented the final design, Ssangyong Cement were very encouraged.
“We could see the HOTDISC-S design compensated for the differences in layout, without compromising on the efficiency of the process,” says Soo-Hyoung Lee. “We were pleased to go ahead with a HOTDISC-S for both our Donghae and Yeongwol plants.”
“This project clearly shows the benefit of cooperation,” says Steven Miller, FLSmidth. “Ssangyong Cement saw the potential of the HOTDISC to give them the ability to burn more alternative fuels and they trusted us to come through with a design that suits their layout. And now, any other plants operating an SLC calciner also have the option to increase their utilisation of alternative fuels thanks to Ssangyong Cement’s support.”
Surpassing expectations
The actual results have surpassed expectations. The guarantee of 85% waste fuel replacement in the calciner with SRF was
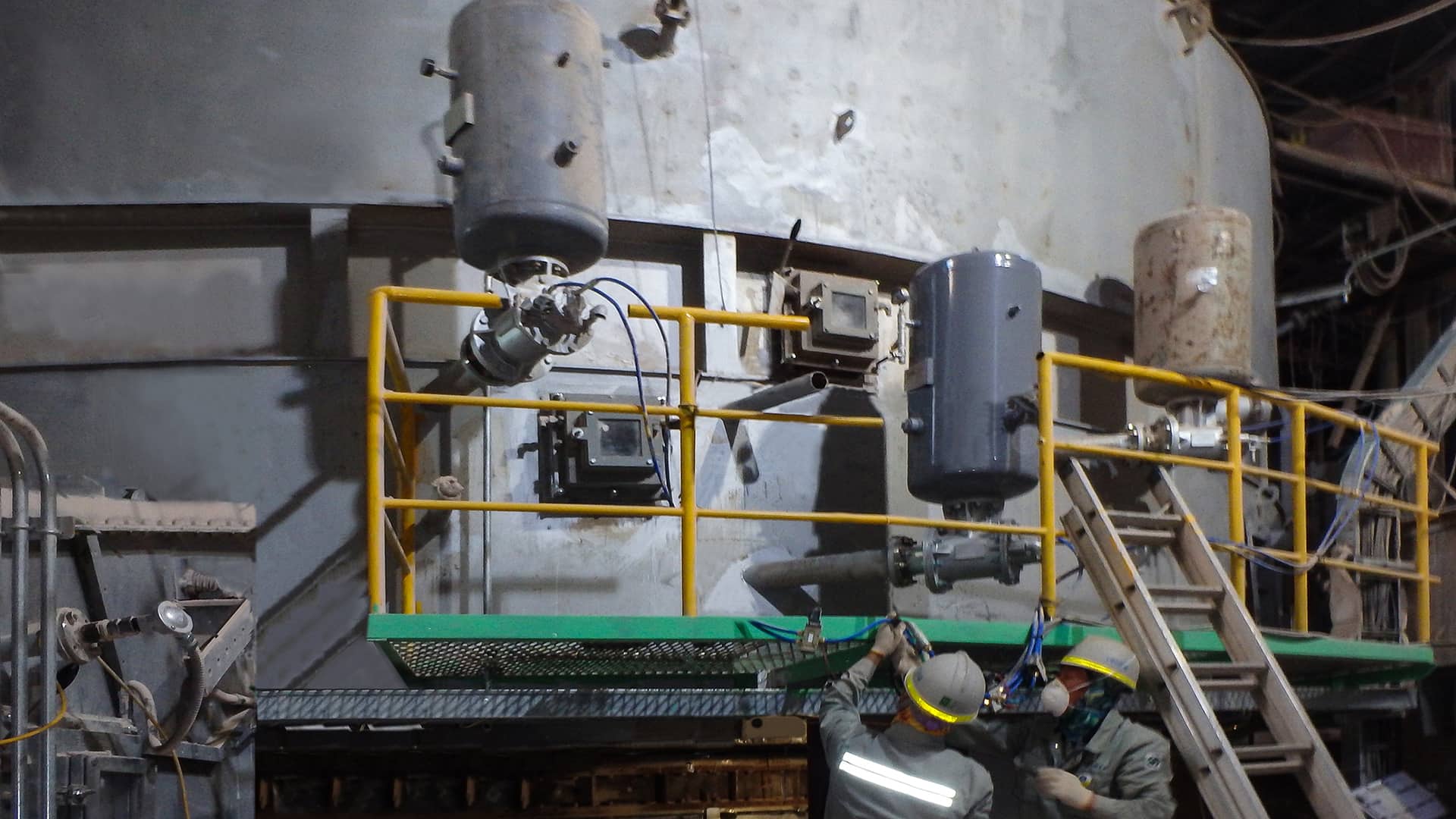
The Donghae cement plant
The Donghae Plant is the world’s largest cement plant with an annual clinker production capacity of 11.5 million t. Located on a 2780-acre site, including the quarry, the plant has had the quality of its product accredited by many expert institutions both in and outside of the country.
About Ssangyong Cement
Established in May 1962, Ssangyong Cement has grown to become the largest cement manufacturer in Korea and now produces 15 million tons of cement and clinker at its four plants in Donghae, Yeongwol, Mungyeong and Gwangyang. The quality of its product is recognized internationally and the Company’s exports account for about half of the country’s entire cement exports.