Our alumina GSC features a vertical cylindrical design in which fuel is combusted in an external air heater. As fine ore (typically less than 1mm) is introduced above the GSD venturi, it directly contacts hot gases from the external air heater. Immediately entrained in the hot gases, the ore dries in seconds. Dry ore and spent gas then separate in a cyclone. Spent gas and dust report to a dust collector, and the gas vents to the atmosphere. The underflow from the cyclones and dust collector report as product.
The number of stages in the system can be custom designed, based on the materials being processed, process requirements, thermal and system efficiency optimisation and capacity. In addition, to preheating stages, cooling stages may also be incorporated to maximise heat recovery and limit downstream cooling requirements.
A closer look at our GSC components
Dust transport is a common cause of excessive power consumption. By eliminating the need to use compressed air, our newly developed transport system requires minimal power to transport dust particles back to the GSC system.
Our redesigned holding vessel (HV) provides the ideal retention time for solids to achieve the desired product quality. This new optimised design eliminates common deadstock issues and provides higher thermal efficiency, more reliable fluidisation and prolonged refractory life.
An improved cyclone design prolongs vortex finder life due to less wear on the equipment. A lower gas velocity in the cyclone reduces both pressure drop and wear on the vortex finder, which minimises the risk of particle breakdown. A shorter cyclone height helps to reduce the footprint and the building height. Fewer raw materials required for building further reduces your capital requirements as tied to structural costs.
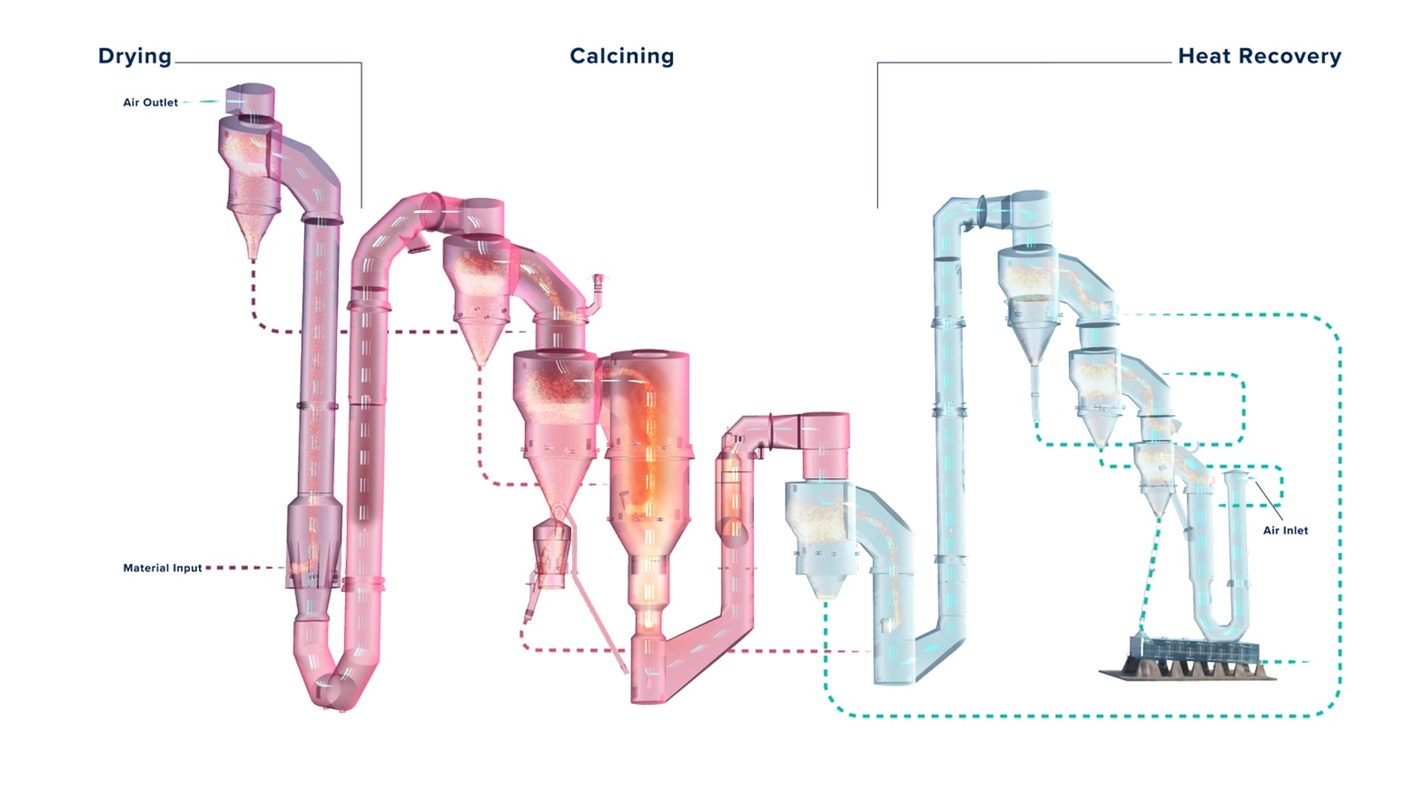