In 2019, a customer in Kazakhstan was seeking a new type of service agreement level from FLSmidth – one that would provide the foundation for continuous and sustainable improvement for their organisation and the local mine. The idea was to implement a new structured framework for training and competency assessment, called the Local Knowledge Transfer Programme.
By training employees in operations and maintenance knowledge on FLSmidth equipment and solutions, the customer was aiming to optimise their resource inputs, cut downtime and minimise waste.
Since 2016, FLSmidth had been on site with a Technical Advisory Services Contract (TAS) and was well positioned to propose a complete solution for the customer. In a short time, schedules and planning were developed for an 18-month period during which two training sessions on each of the FLSmidth products at the site would take place.
Training that delivers cost benefits and reduced downtime
After each training, a structured knowledge assessment phase for candidates would take place, allowing the customer to view an accurate assessment of each candidates’ product knowledge. Based on this, the customer would evaluate competency levels across their local teams and prioritise any additional training or work experience exposure.
This focused training and experience was designed for more efficient planning and maintenance in the long term; it would be a valuable and sustainable pathway to lower overall cost of production due to increased equipment availability, unplanned downtime reduction and maximised product component and spares life.
At the end of the 18 months, the programme would promote our FLSmidth Kazakhstan service employees into our key TAS leadership positions. This is to increase local team engagement, increasing sustainability and reducing the expense of fly-in, fly-out regional personnel. The result is a direct cost benefit for the customer, while maintaining the quality and provision of FLSmidth Supervision.
Getting the Localisation Programme into motion
So how did it all get started? To ensure alignment from the get-go, the customer assigned a programme engineer to work alongside the FLSmidth Lead Programme Development engineer (LDPE). They conducted an analysis of internal training needs, recommended candidates to take the course, reviewed and approved all FLSmidth-produced training materials and formats, aligned schedules and planned next steps after the FLSmidth assessment of candidates.
In conjunction with the customer, it was decided that the LKTP programme would consist of operations and training modules for each of the key products, including gyratory crushers, cone crushers, SAG and ball mills, conveyors, flotation cells, pumps, cyclones & valves, filter presses, thickeners, ABON crushers, the VXP and onstream analysers. Materials for the training were compiled over nine-month period as an FLSmidth bi-regional project group.
All materials were designed to train and enable a candidate to become well experienced in the maintenance of the equipment and have the ability to carry out all tasks unsupervised. Candidates also acquire the necessary skills to lead a maintenance team in the safe removal and replacement of equipment components and complete all necessary reports and documentation.
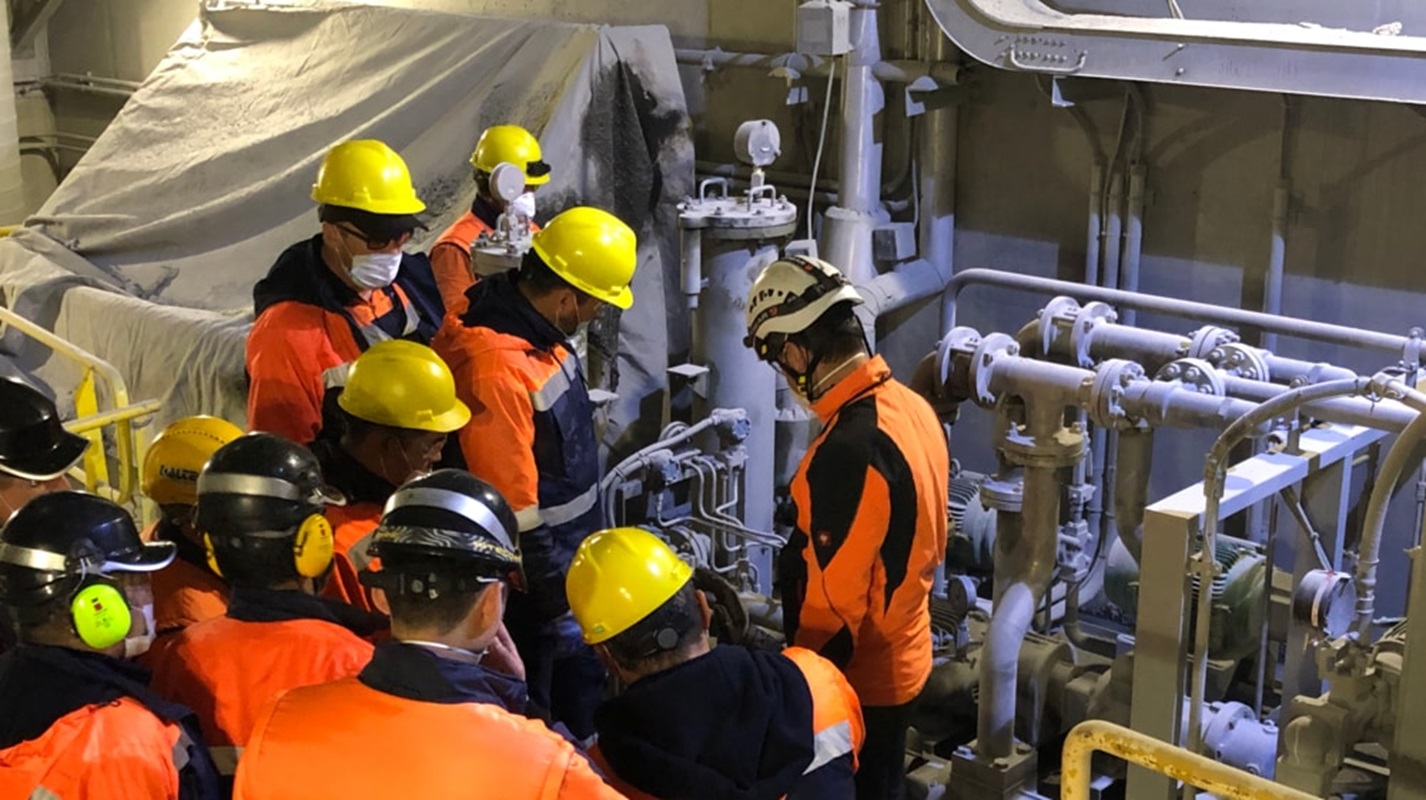
The practicalities
The 10-to-12-day on-site training session combines the product training and individual candidate assessment. These sessions have been structured to suit the customers rotation schedule, with class sizes usually around 14 per session. The customer required the training to be part of their normal shift rotation patterns. FLSmidth’s local engineers in Kazakhstan, also on same shift patterns, attend the courses for alignment and training purposes.
Current progress
The first physical site product training module with assessment was delivered in August 2021 and the trainings are currently ongoing, with half of the Phase 1 product courses delivered to date.
After each training and assessment, a formal participant survey is conducted using the Kirkpatrick system. While the overall programme targeted a score of 3.8, current evaluations are at an average of over 4.9 out of 5. With such clear, early success, similar LKTP programmes are already being discussed with the customer.
With training materials now developed and prepared for equipment across the flowsheet, future trainings can now be rolled out faster at other locations or for other customers. In fact, the main planning needed is to align needs and schedules with the customer due to the practical and in-depth nature of the modules and one-on-one assessments.
Customer benefits
Customers are increasingly interested in ensuring local staff continuously develop and improve equipment knowledge. Effective knowledge transfer to customer maintenance and operations teams is a key tool that allows them to run efficiently, sustainably, and with the lowest cost for their operations.
This programme format demonstrably adds to FLSmidth’s commitment and desire to deliver its service locally through our customer-site facing engineers and employees. For our customers, having FLSmidth people or FLSmidth-trained people onsite or close by 24/7, means they can tackle any issues quickly and efficiently, eliminating the risk of having to wait for external support.
The end result is the ability to bring equipment back online quicker, while due to better continuous maintenance, the customer can also reduce the overall risk of downtime.
If you are interested in a similar “super-charged” service agreement with training and full assessment, please start by talking to your local FLSmidth contact.