The largest cement plant in Turkey trusts FLSmidth with a complex multi-phase installation project, including of non-FLSmidth equipment. Comprehensive installation services and a wealth of experience and expertise make FLSmidth uniquely positioned to successfully deliver jobs of this scale.
Challenging job increases in scope
Nuh Çimento, which was founded in 1966, is the single largest cement plant across Turkey and Europe. This mega plant has three lines and includes two non-FLSmidth kilns and an FLSmidth Rotax-2® kiln. It has an annual production capacity of 4.4 million tonnes of clinker and six million tonnes of cement.
Nuh Çimento required kiln specialists, girth gear specialists, and ultrasonic welding specialists, as well as strong project management, technical advisory services and contracting, to successfully complete all the components of this huge project, which initially started out much smaller in scope.
"This project became several challenging projects at once. None of the other suppliers could offer us what the FLSmidth team could - global expertise and a very strong local setup, which was invaluable."
CÜNEYT DILSIZ
Mechanical Maintenance Manager, Nuh Çimento
Matching expectations
Gradually, the job became several activities that needed to be executed within one larger project. Nuh Çimento required a reliable partner with vast experience to manage this complex project and deliver it within the required timeframe, with minimum downtime.
“With their local setup in Turkey, including kiln and gear experts, FLSmidth was the only one who could match our expectations for this expanding job,” explains Mr Cüneyt Dilsiz, Mechanical Maintenance Manager at Nuh Çimento. “FLSmidth had the necessary insights, skilled people, resources and parts ready to start and to complete the installations with minimum downtime and no unexpected delays.”
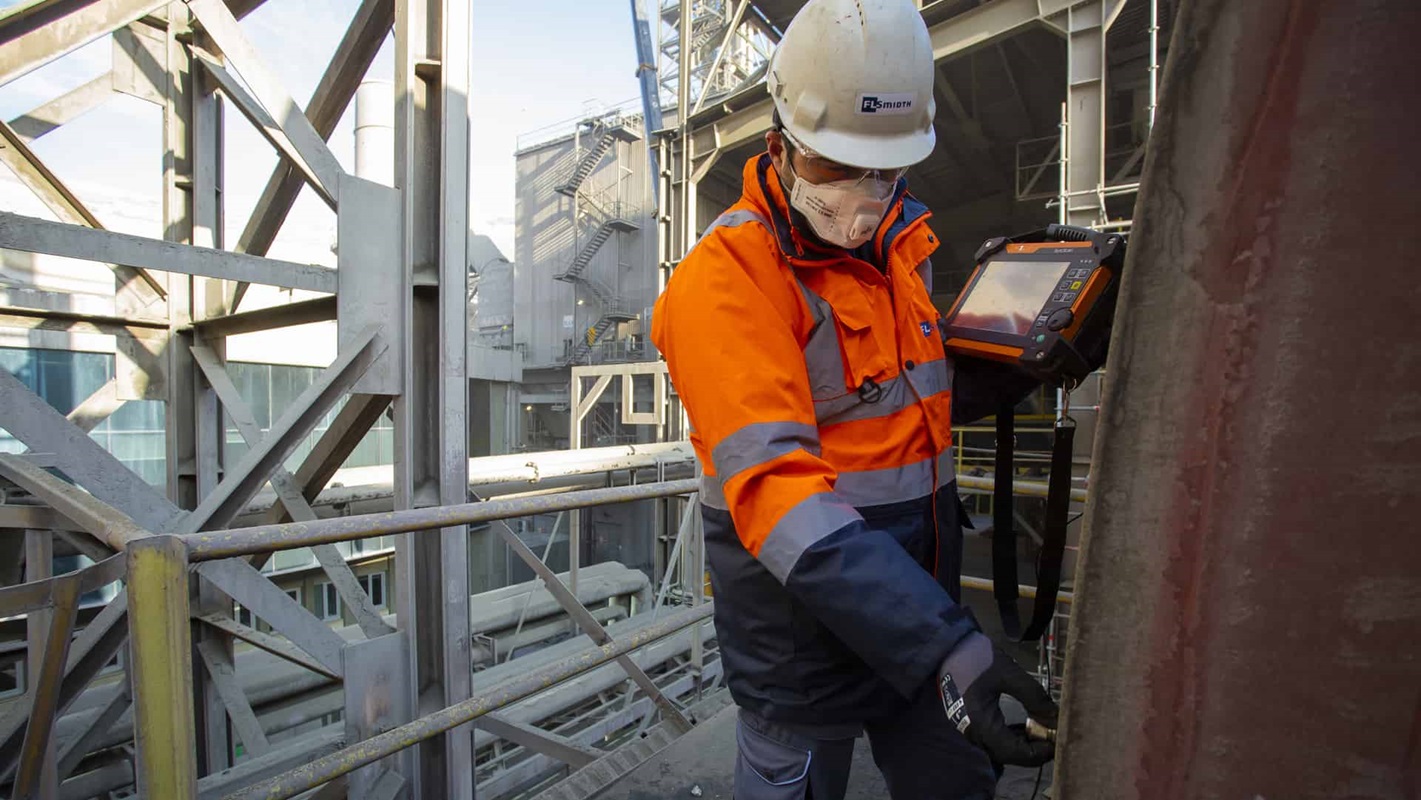
Readiness to start
By 2020, the scope had increased considerably, and the task had become almost a turnkey project. It consisted of 14 kiln shell sections – totalling 42 metres, including heavy sections and live rings, girth gear-pinion replacement and alignment, individual before/after hot kiln inspections, and all welding NDT/ultrasonic tests, as well as all project management and technical advisory services.
Mr Cüneyt Dilsiz, continues: “This project became several challenging projects at once. None of the other suppliers could offer us what the FLSmidth team could - global expertise and a very strong local setup, which was invaluable.”
"We really valued the ability of FLSmidth to be able to schedule this job so quickly. They were working with us closely and were 100% ready to start on short notice."
CÜNEYT DILSIZ
Mechanical Maintenance Manager, Nuh Çimento
In February 2021, less than one month after the final contract was signed, the FLSmidth team began the job. They started with pre-assembly, which took 30 days. The next phase included dismantling and installation. After 18 days, the kiln installation was completed with the final girth gear alignment - four days earlier than agreed. The comprehensive kiln inspection took place after kiln fire up and was finalised with kiln alignment.
“We really valued the ability of FLSmidth to be able to schedule this job so quickly. They were working with us closely and were 100% ready to start on short notice,” says Mr Cüneyt Dilsiz.
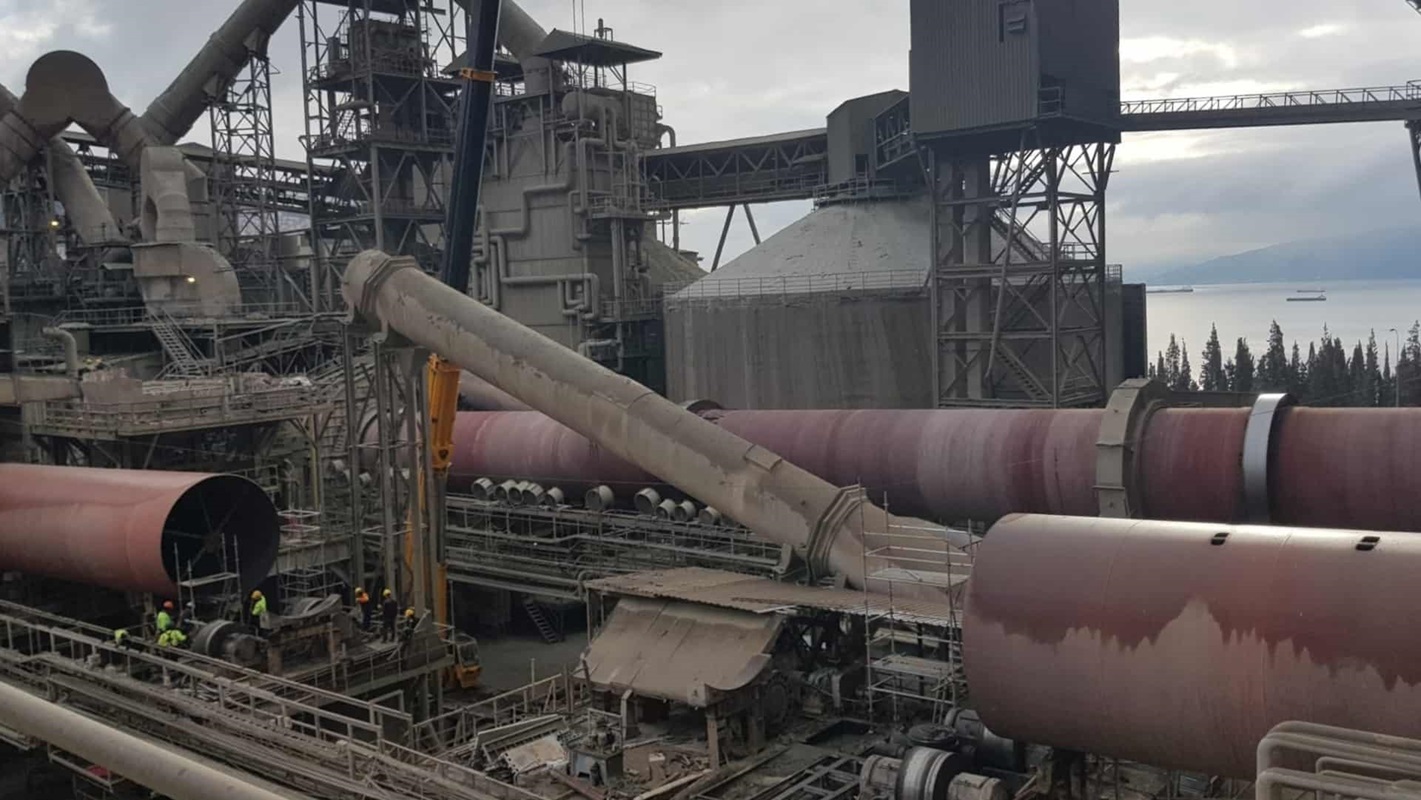
This readiness to schedule the job and have the right people, resources, planning and parts available is, in part, due to the strong local team: FLSmidth has 42 people working in Turkey with a wide range of competences. “Responding quickly with the right qualifications and people is possible due to our global reach and strong partnership with our closest customers,” explains Mr Zeki Kozanoglu, Managing Director, FLSmidth Turkey. “It has enabled us to be a reliable partner in the local cement market.”
The scope of the project included:
- 14 kiln shell replacements – totalling 42 metres
- 3 supports- all heavy section replacements
- 3 supports- all live ring replacement
- Girth gear shell replacement
- Girth gear and pinion replacement
- Comprehensive kiln inspection
- Supervision during pre-assembly (30 days)
- Supervision during assembly (22 days)
- Health and safety supervision (52 days)
- Kiln axial alignment
Duration of kiln installation:
- Pre-assembly: 30 days
- Assembly: 22 days scope, but only took 18 days in total
Keeping everything on track for success
This extensive task required strong project management to keep everything on track. Trust in FLSmidth played an important part and Nuh Çimento relied on the expertise of the team, including a kiln specialist, girth gear specialist, and ultrasonic welding specialist - all working together to ensure a smooth installation. Having one point of contact meant that Nuh Çimento minimised the risk of delays and avoided increasing the complexity of this already challenging job.
Jens Peter Koch, Vice President for Europe, Russia & North Africa at FLSmidth, further comments:
“Our skilled local specialists, supported by our international teams, prioritise your plant productivity and sustainability – making us your strategic service partner of choice. We’ll deliver the quality services you need, in the shortest timeframe, helping you effectively maximise availability and optimise production.”
"Our skilled local specialists, supported by our international teams, prioritise your plant productivity and sustainability – making us your strategic service partner of choice."
JENS PETER KOCH
Vice President for Europe, Russia & North Africa at FLSmidth
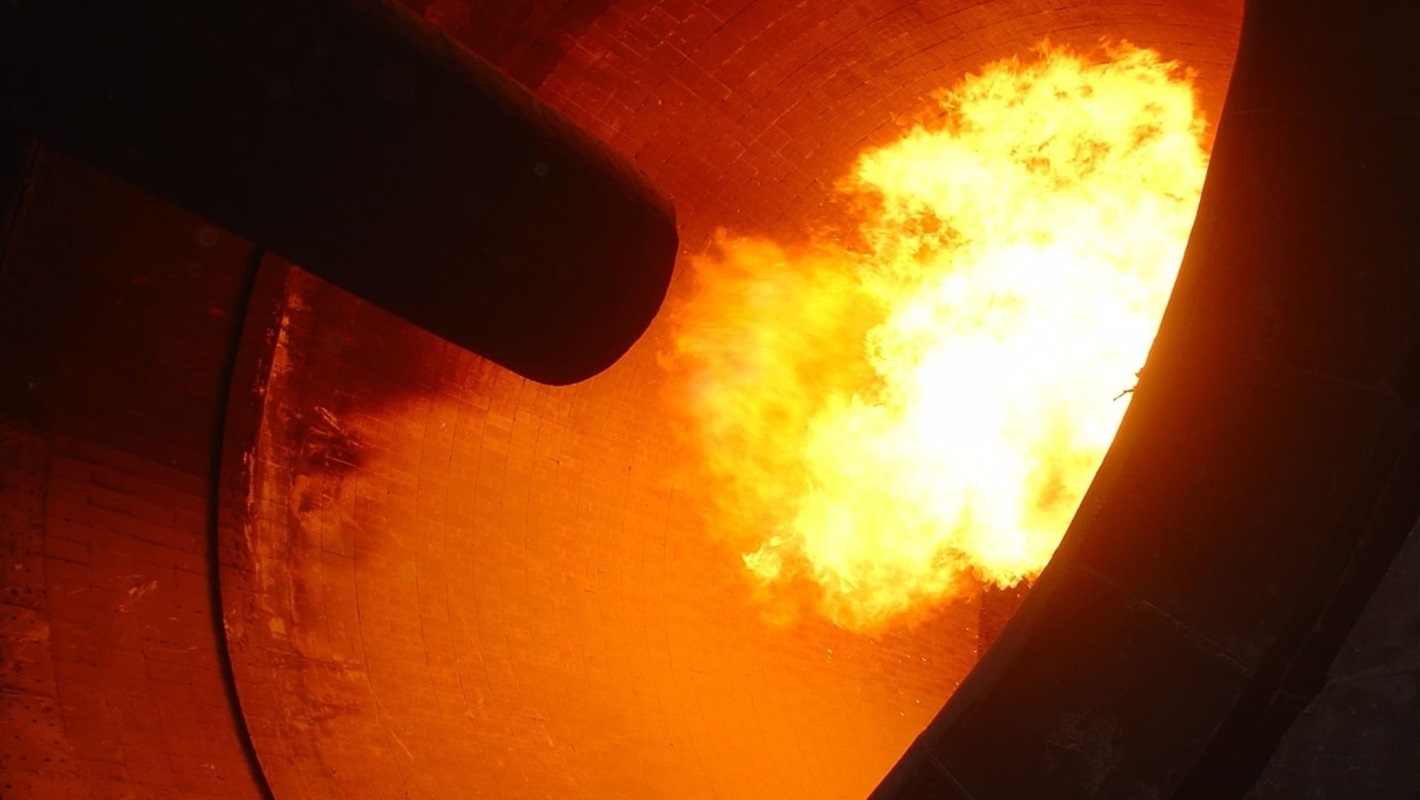