Remote support enables cement producer to optimize plant performance
“As a new player in the industry, they wanted to make sure they were producing a high-quality product, efficiently, safely and in an environmentally responsible manner. Process optimization is not just for older plants – it was always part of their plan.”
MORTEN TOFT, GENERAL MANAGER – PRODUCT SALES, SUB-SAHARAN AFRICA, MIDDLE EAST AND SOUTH ASIA
FLSmidth
The plant wanted a solution that would enable them to operate with minimal fuel and power consumption and low emissions. With quality control also a priority, they wanted an advanced automation technology that could minimise the potential for human errors and contamination in laboratory operations. In addition, as a new entrant to the market, they wanted the support of process experts on call 24/7.
“Their relationship with FLSmidth was well-established by this point. We supplied all the major equipment for the plant, and they knew we could help them get the most out of it. We entered into a remote support agreement that incorporates some on-site inspections and assistance.”
ALTRIN PRABAHAR, PRODUCT AND SOLUTION SALES, SUB-SAHARAN AFRICA, MIDDLE EAST AND SOUTH ASIA
FLSmidth
The agreement the customer has chosen includes support and maintenance of the plant’s control system, CEM Scanner and RoboLab, as well as maintenance support for all key equipment.
Key to the contract is PlantLine®, the service agreement that helps plant managers and operators make the most of their FLSmidth automation systems. PlantLine® gets its name from the 24/7 support line that links plant operators with process experts by telephone, email and remote connection where applicable. This isn’t only an emergency service – it’s available to plant operators who have questions about performance optimization, who are looking for advice or suggestions, or just want someone to bounce ideas around with. The PlantLine® service agreement for the plant’s control system and CEM Scanner also enables FLSmidth’s engineers to access the plant’s network to make urgent modifications to the system when needed. Software maintenance can also be managed remotely, as can key security measures such as antivirus and firewall protection. The RoboLab PlantLine® agreement additionally includes annual maintenance visits, enabling FLSmidth and our technical partners to assess equipment and performance in person.
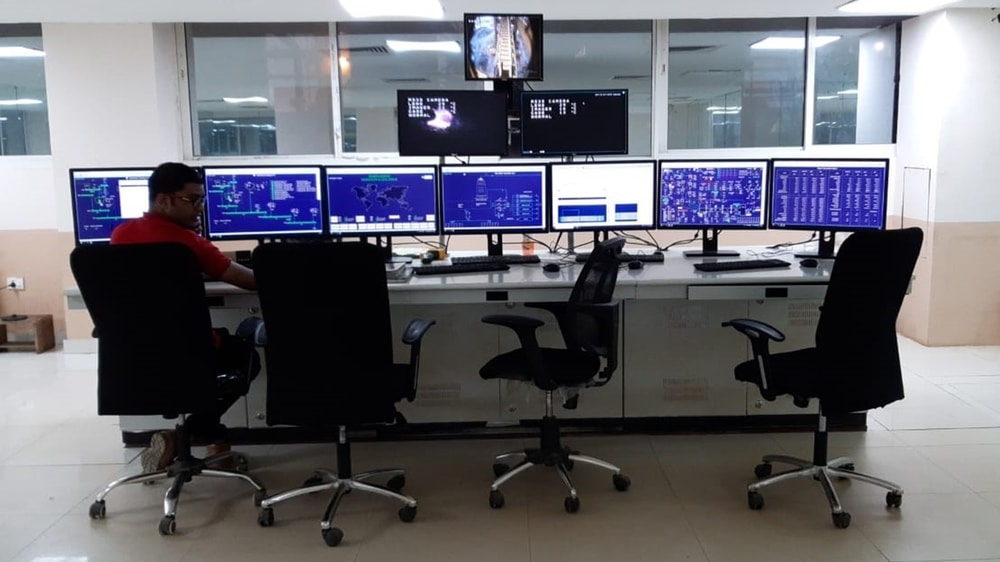
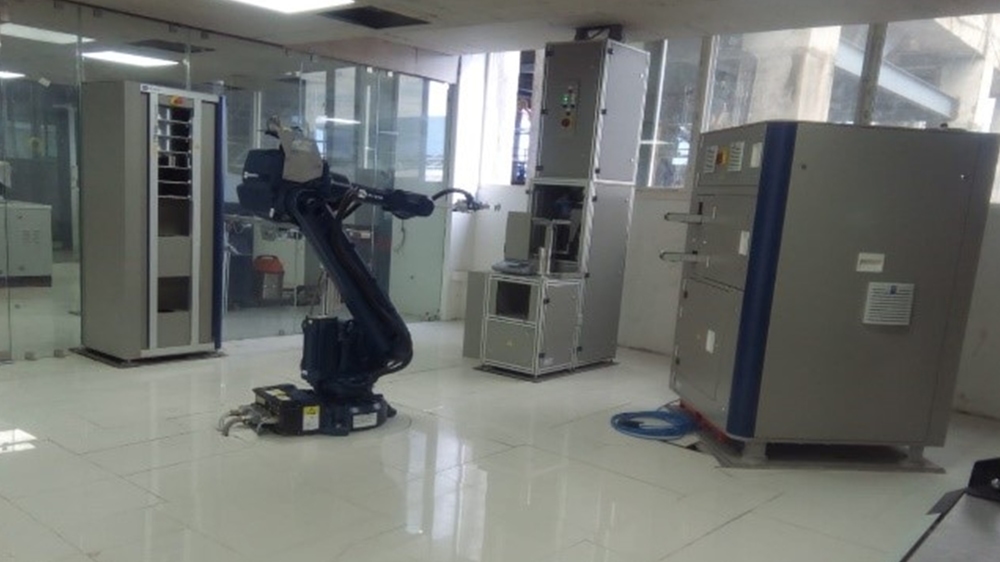
“Our remote support services have proven to help customers reduce operating costs and increase performance.”
MORTEN TOFT, GENERAL MANAGER – PRODUCT SALES, SUB-SAHARAN AFRICA, MIDDLE EAST AND SOUTH ASIA
FLSmidth
“As a technical partner to many cement producers worldwide, we have the benefit of a wide range of experience across different raw materials, different regulatory environments, etc. That, in combination with the process expertise we’ve gained through testing and developing our equipment, puts us in a strong position to advise cement producers on how to minimise emissions, reduce fuel and power consumption, and cut costs, all while improving productivity and performance. The fact we can do this remotely is a huge benefit, enabling more immediate action and support at a much lower cost,” says Morten Toft.
PlantLine® benefits include:
- Reduced downtime-related costs
- First priority status
- Fixed maintenance cost
- Improved system performance
- Higher run factor
- Extended system lifetime
- Lower risk
- Improved productivity and quality with the Performance Monitoring and Remote Optimisation module.
In addition to the PlantLine® service agreement, FLSmidth is also undertaking process monitoring of all equipment from the crusher to the cement mill. This Smart Support Package comprises:
- Monthly calls
- A single point contact for all service requirements
- Spare parts forecasts and inventory planning
- Measuring the maintenance impact
- Reports and recommendations
“The pandemic limited the plant’s access to local resources, and they were finding it difficult to stabilise their process and optimise performance. Having experts on call 24/7 has enabled them to make the most of the equipment they invested in, get more out of their materials, and improve operational efficiency.”
ALTRIN PRABAHAR, PRODUCT AND SOLUTION SALES, SUB-SAHARAN AFRICA, MIDDLE EAST AND SOUTH ASIA
FLSmidth
The FLSmidth-supplied line was commissioned in early 2020 and includes:
- ATOX Mill 35 for raw grinding – 180 tph
- ATOX 17.5 for coal grinding – 20 tph
- 2200 tpd energy efficient pyro line including the latest Cross-Bar® cooler and Jetflex burner
- OK mill for cement grinding – 100 tph
- Complete plant laboratory automation with QCX/Robolab® systems